NiceFlow Turbo is a new tool and a technological breakthrough in the general landscape of CFD, and in the sector of Turbomachinery in particular.
What new features does NiceFlow bring?
NiceFlow carries out certified simulations without any numerical error due to non-optimal meshing. This is particularly recommended in aerospace, automotive competition, and everywhere where the benefit of a few percents is crucial.
We work exclusively with anisotropic tetrahedral mesh. Whatever the complexity of the geometry we directly have a perfect meshing of it and in addition an optimal meshing for the CFD simulation. Unlike structured meshing approaches (hexa, pyramid, prisms) our meshing never fails even for very complex geometries.
The optimal mesh is calculated automatically by coupling with the fluid solver including the boundary layers meshing with no slip or law of the walls. The Y+ of the first mesh at the wall is well calculated around 1. As a consequence, the engineering time is limited to a few minutes and the result is perfect. Please not our approach is not based on guidelines and rules for calculating empirical mesh size, it is entirely mathematical based on a calculation of the error of the solution.
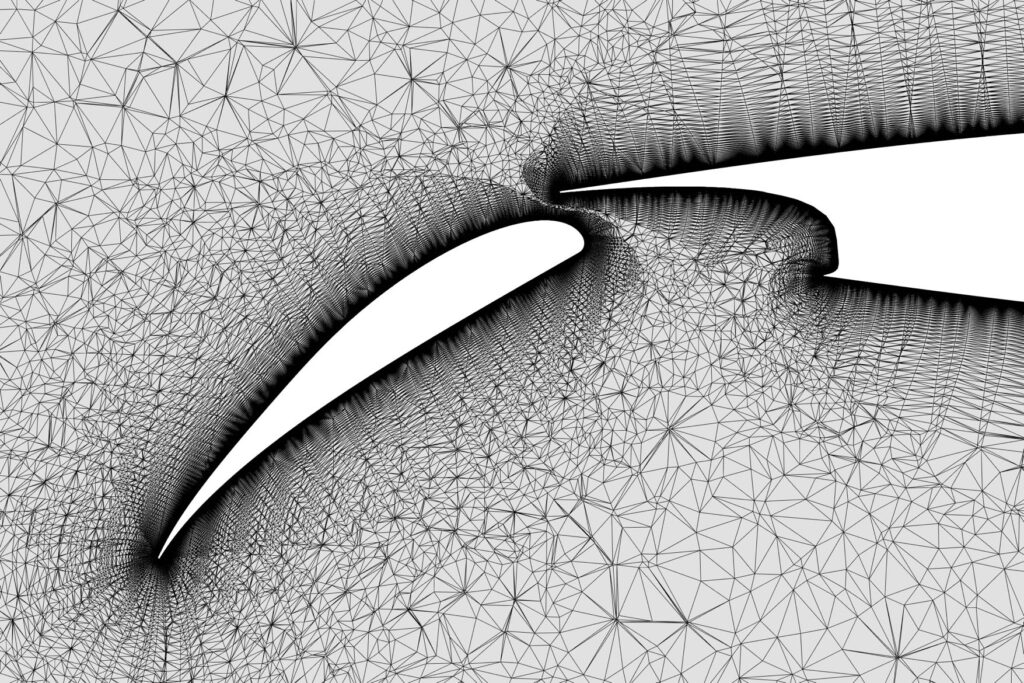
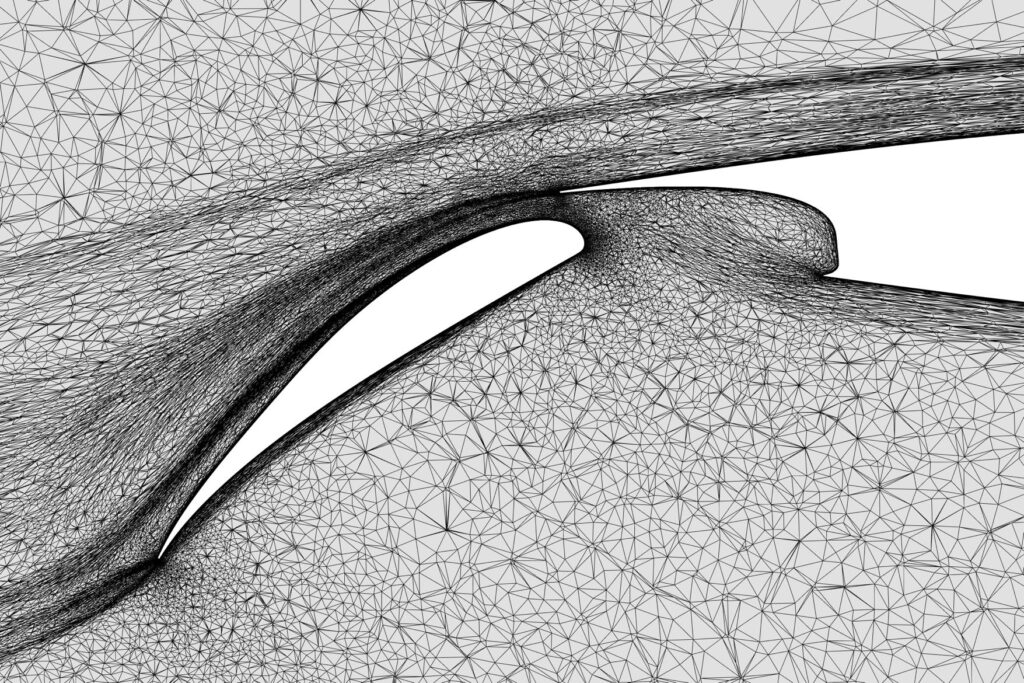
The CPU time consumption on a conventional cluster is ten to fifty times one faster than our competitors.
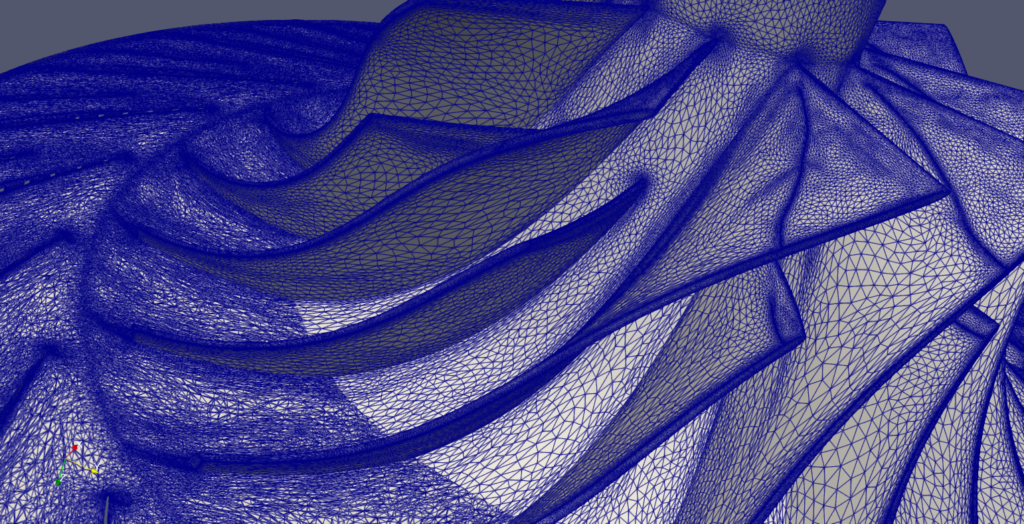
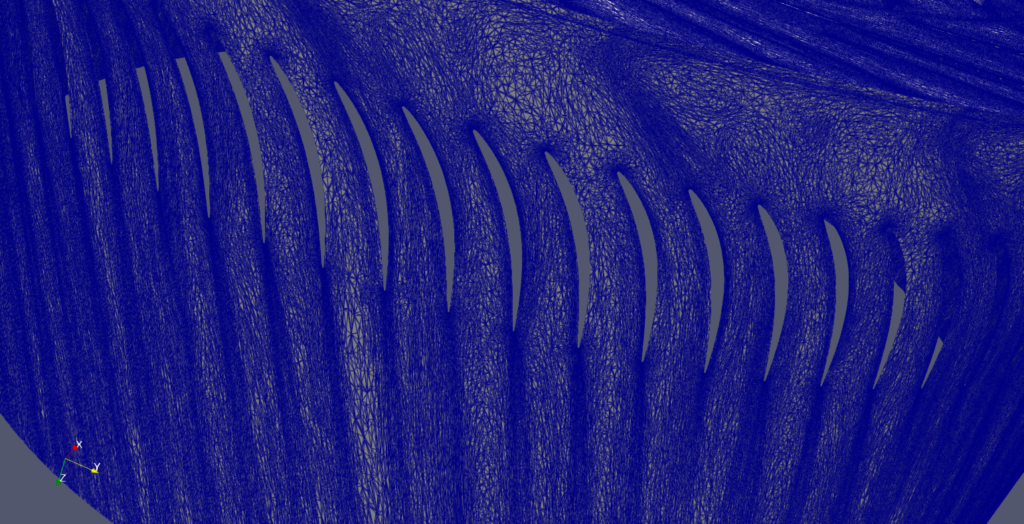
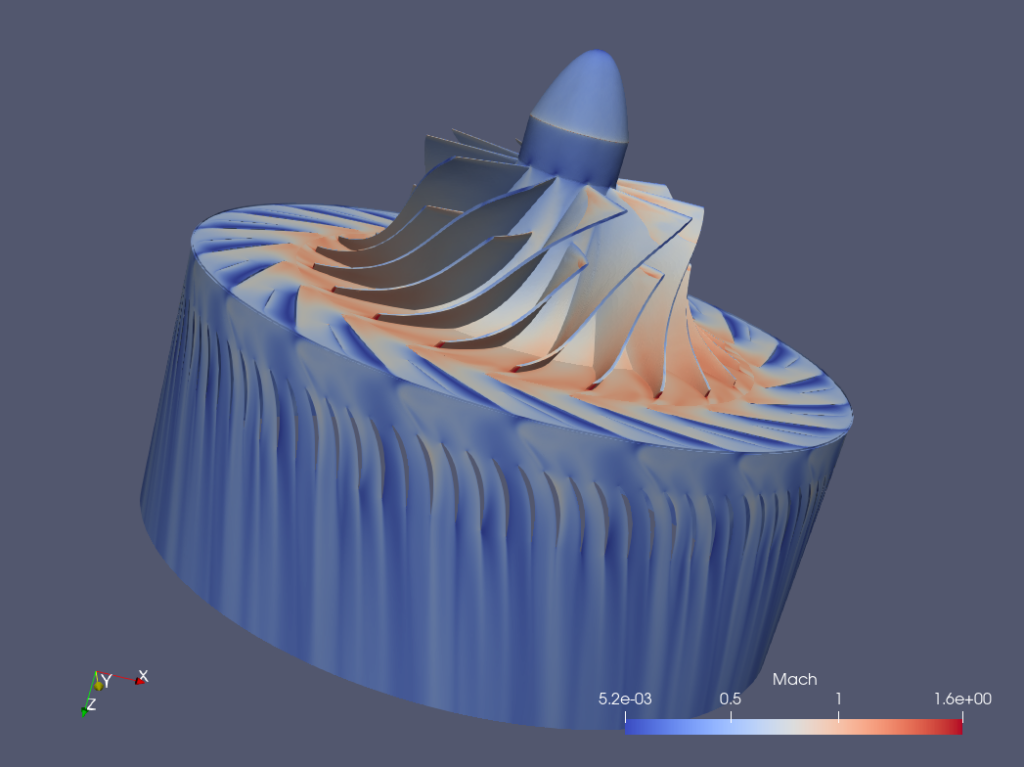
Accuracy
What could be more accurate than optimal mesh adaptation based on error estimator? It is the most advanced technology to date for delivering high fidelity calculations, there are no more errors linked to the meshing and the mesh is calculated automatically by the solver, no intervention from the engineer.
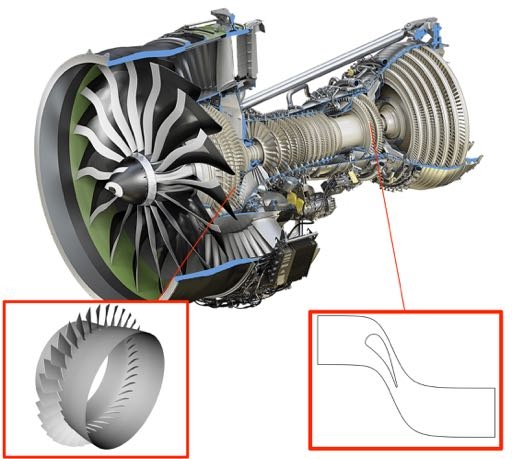
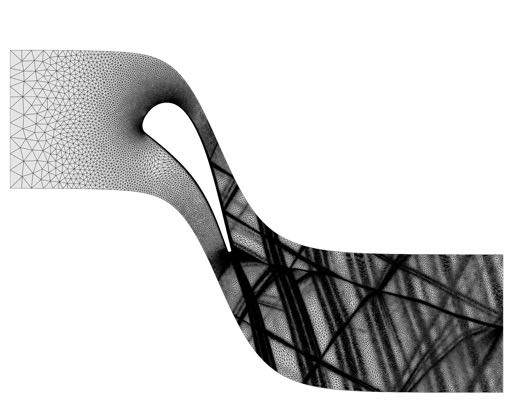
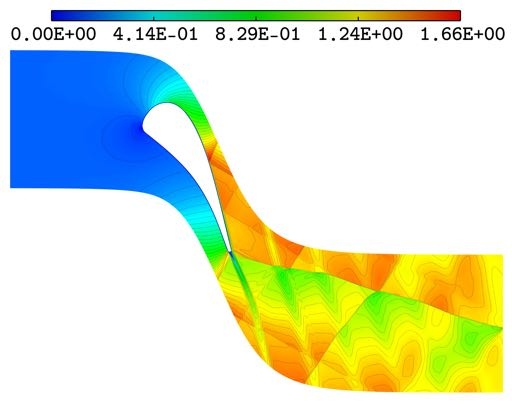
As a rule, current meshing and solver tuning require the translation of years of experience of experts to be and translated by software editors into guidelines.
With our technology, no more need of guidelines: the meshes are calculated mathematically with the help of the fluid solver. Complicated simulations can be handled directly by beginners, as for the experts, they can devote themselves to analyzing the results without wasting their time on thankless and time-consuming tasks.
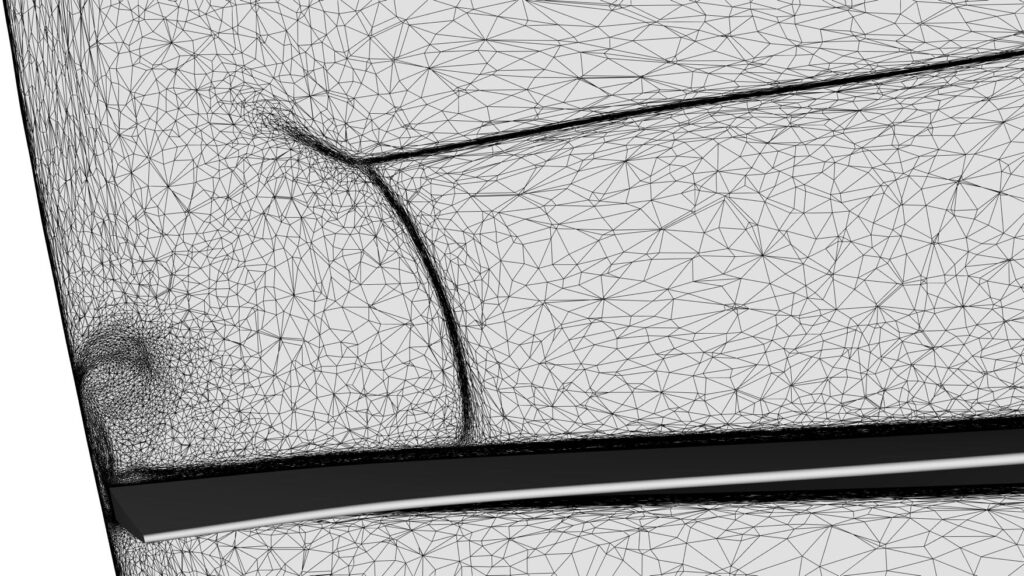
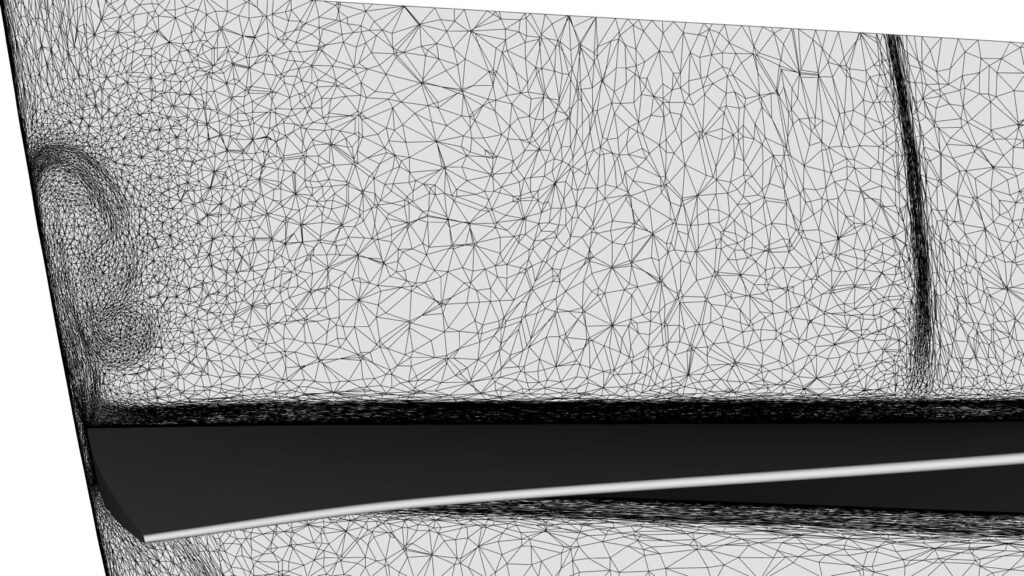
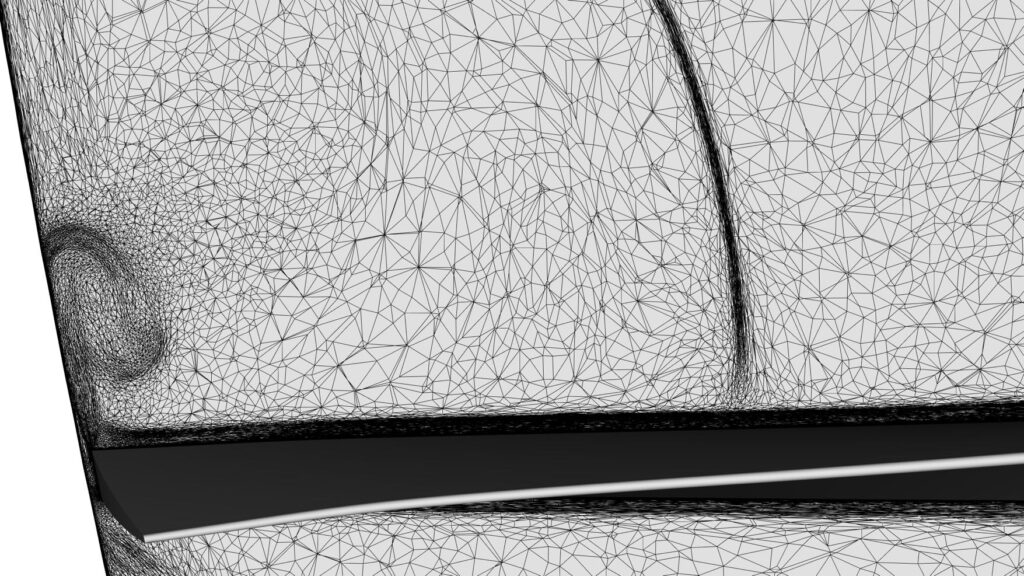
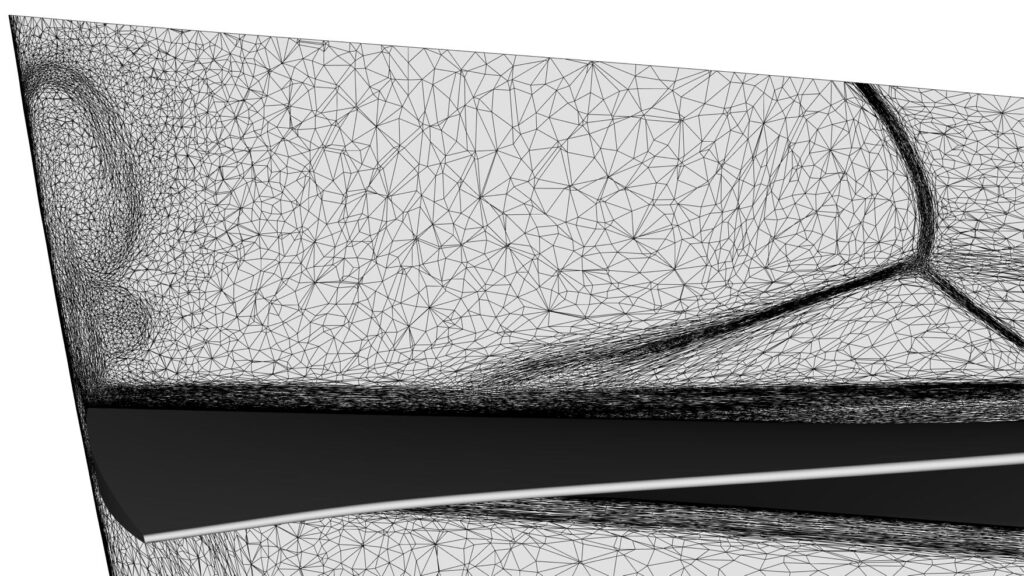
If you have already optimized your design, entrust it to us, you will gain even more performance!
In fact, if you think you can optimize a design based on a fairly inaccurate CFD calculation, you are wrong! The shape gradient is very sensitive to the solution and will provide very little or no benefit if your solution is not very accurate, which means that your design is far from perfect!
Our optimization approach based on adaptive mesh has four major advantages:
- It allows to optimize a complex geometry with a huge distortion during the optimization process without any difficulty.
- The optimal shape is always calculated on an optimal mesh and not with the initial mesh used to calculate the solution.
- We use an adjoint method to calculate the shape gradient, this is the most efficient way to optimize in terms of accuracy and CPU time with any number of shape parameters.
- Our optimization process is CAD to CAD: you start your optimization with the initial CAD of your geometry and the result of the shape optimization calculation is a CAD of the new geometry.
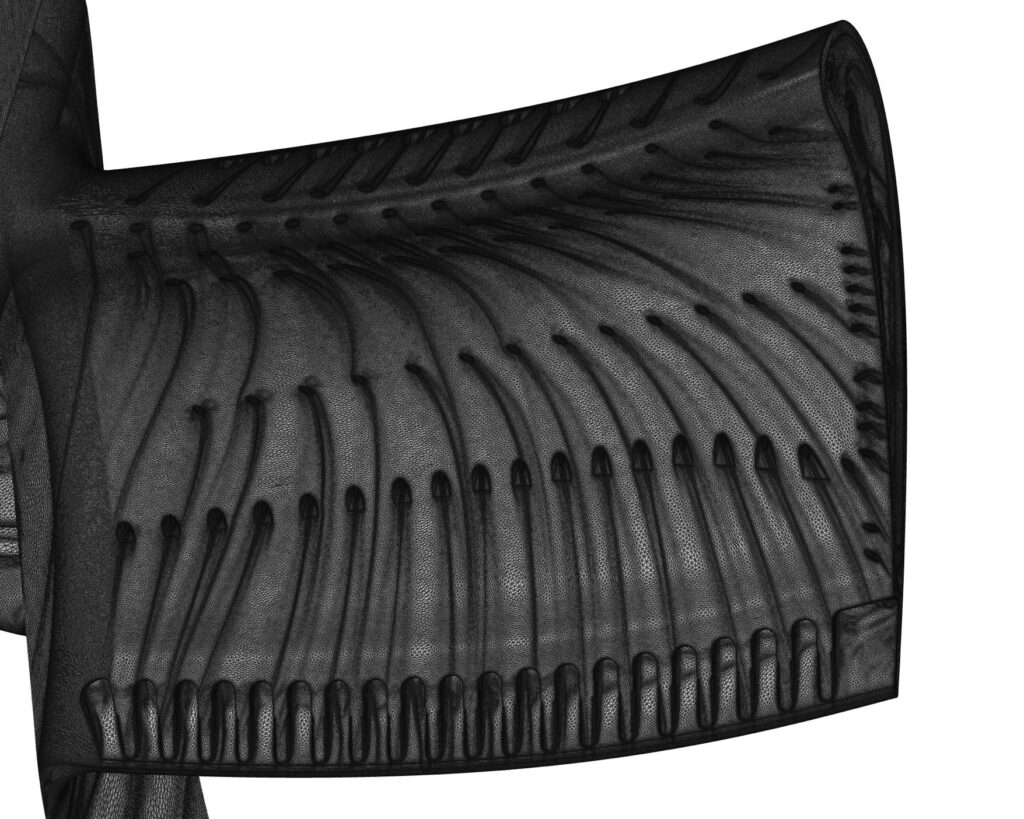
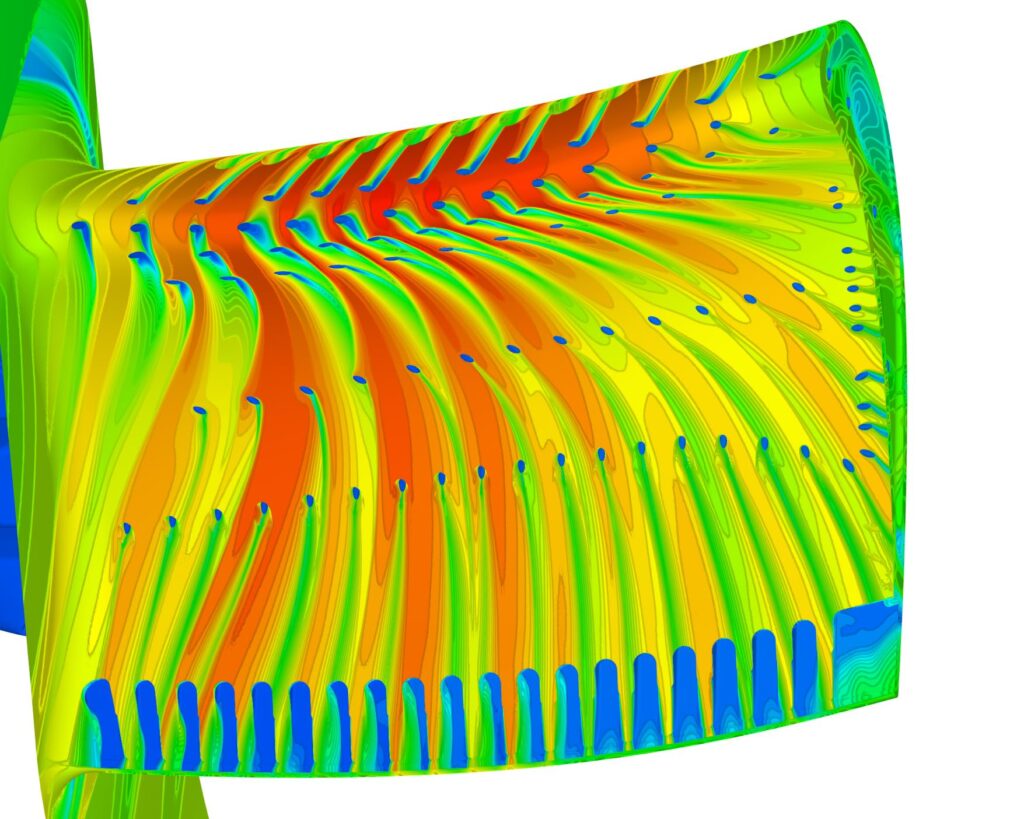
NiceFlow is able to simulate:
- Aero engines and gas turbines.
- Turbochargers.
- Hydraulic turbines.
- Propellers.